What Is Manual Flange Facing Machine and Its Other Factors?
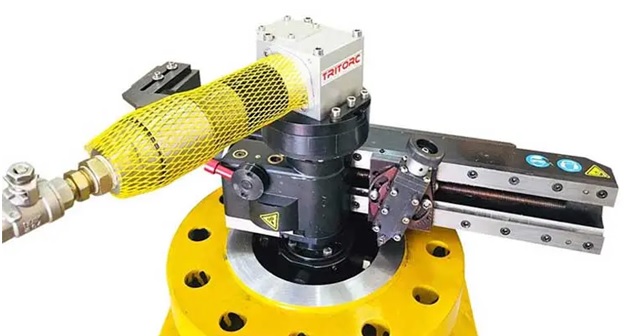
Flange facing is necessary to guarantee that old flanges remain operational without any problems with their joint integrity. During the repair and maintenance period, flange surfaces are machined as part of the flange-facing process. Flanges must be adequately maintained and repaired to prevent leaks and corrosion, extending their useful lives. Therefore, a manual flange facing machine needs to be used properly.
What is flange facing?
By resurfacing the flanges with machining, a perfect seal is created when assembled. This process is known as flange facing. A flange going to face tool, rubber gasket facing device, or flange facers is used to perform flange facing. Flange facing machine manufacturers provides qualitative machine which comes with different attributes. They are mainly used in oil and gas, petrochemical, refinery, pharma, pipeline, food manufacturing, pesticide, and energy production companies, and flange facing is a crucial process.
What Makes Flange Facing Necessary?
Flanges constantly experience damage from turbulent flow because they are under pressure while in use. Additionally, they sustain cuts from gasket leaks or impacts with the other components during construction and installation. As solutions are forced to follow a spiral route rather than traverse the flange face, flange facing cuts these same flanges and provides a spiral recessed finish that makes flanges less prone to leaks. One of the most crucial repairs is flange facing, done during plant closures or maintenance activities.
Machine for Facing Flanges:
A flange-facing machine is beneficial for mechanically cutting or polishing discs, necklines, rings, or flanges. In the piping industry, flanges frequently become damaged during use or handling. These damages are eliminated using a split screen cutter widely recognized as just flange-facing equipment to guarantee the integrity of the flange joint. Due to their ability to repair flanges of any radius without replacing them, flange-facing machines are also referred to as portable lathe machines.
Flange-facing machine operation:
The flange-facing machine’s scalpel blade removes destruction from the flange face by moving across it in a spiraling motion. To that very uniformity and regularity, this cutting or polishing procedure is done in successive strips. After the flange facing is complete, the flange’s performance and appropriate sealing ability are realized.
Using geared fixed channels, finishes meeting ASME B16.5 requirements are produced. The operation of flange-facing machines is adaptable. They can be installed at any angle, even with their orientation reversed. When not mounted laterally, the flange facer’s facing arm has been balanced using movable weights.
Different applications of it:
- Fixing phonographic finish, elevated face, and flat facial expression flanges
- Milling, digging and facing of ship thruster mount
- Repairing the mating flanges on piston rods
- Feed crank flanges for boilers
- Ring groove fixing or the creation of new grooves
- Preparation for welding on vessels and plates
- Ship trapdoor sealing surfaces refaced
- Re-machining the rotary job correctly’ bearing surfaces
- Restore heat exchangers and refacing of valve flanges
- Section of a wind tower puttering a flange
The following steps are typically included in the flange-facing process:
- The rubber gasket face surface should be cleaned
- Using a cutting tool when machining
- Low feeding and low rotation
- Add machining for fine work