Centrifugal Compressors for Air Management
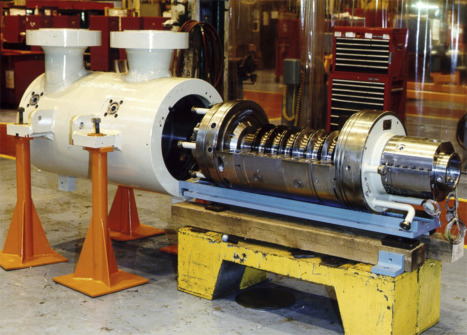
Compressed air has been used for many years and is now one of the major components of several industrial processes. From powering machinery to driving actuators in automation and conveying materials, it’s an essential utility that keeps things moving. A reliable and efficient air management system is crucial for smooth operation, and for that, a highly efficient centrifugal compressor is required.
Generating this compressed air requires specialized equipment. Today, in the air compressors and centrifugal compressors industry, Rivair stands out for offering high quality maintenance services and spare parts for centrifugal compressors. This blog explains everything about centrifugal air compressors, from what they are and how they work to their advantages and how to choose the best one for your needs.
Let’s get started.
What are Centrifugal Compressors?
Centrifugal compressors are a type of positive displacement compressor that uses rotating impellers to convert kinetic energy into pressure energy to increase the pressure of a gas. Centrifugal compressors operate on the principle of converting kinetic energy into potential energy through the acceleration of air.
These Compressed air compressors are different from reciprocating compressors, which use pistons for compression. On the other hand, centrifugal compressors employ a continuous, rotary motion. Air enters the compressor through an inlet and is accelerated by the impeller blades. This acceleration imparts kinetic energy to the air, which is then converted into pressure as it slows down in the diffuser section.
Benefits of Centrifugal Compressors
Centrifugal compressors have several advantages over other types of air compressors:
- Centrifugal compressors can operate continuously, providing a steady flow of compressed air, unlike reciprocating compressors, which have a pulsating output.
- They are also capable of delivering large volumes of compressed air, making them ideal for high-demand applications.
- Today, modern centrifugal compressors are available that boast high efficiency rates, which translate to lower energy consumption and operational costs.
- Compared to reciprocating compressors, centrifugal compressors operate at lower noise levels.
- These compressors are designed to have a more compact footprint than reciprocating compressors, which deliver similar air output.
- Centrifugal compressors can be customized for various pressure and flow requirements, making them adaptable to a diverse range of industrial needs.
- Also, these compressors allow for flexibility in system design and future expansion. This means they can be easily scaled up or down to meet an application’s specific needs.
Applications of Centrifugal Compressors in Air Management
Now, let’s understand the various applications of centrifugal compressors in numerous industries:
- Manufacturing: Used for powering pneumatic tools, robots, and various production processes.
- Chemical processing: In chemical plants, they are used for processes like air separation, gas transportation, and fluidization.
- Oil and gas Transmission: Centrifugal compressors are crucial for gas pipeline transmission, upstream exploration, and downstream refining operations.
- Power generation: They are employed in both conventional and renewable power plants for air supply and pollution control systems.
- Food and beverage industry: Compressed air is used for packaging, conveying, and various processing steps.
Choosing the Right Centrifugal Compressor
Here are the important factors that you should consider while investing in centrifugal compressors:
- Air Flow Requirements: Determine the required volume of compressed air, like what volume of compressed air (measured in cubic feet per minute – CFM) you need at what pressure (measured in pounds per square inch – PSI).
- Discharge Pressure: Identify the desired pressure level of the compressed air at the outlet of the compressor.
- Application: What specific industrial process will the compressor be used for? Different applications have varying pressure and flow demands.
- Power Source: Centrifugal compressors can be powered by electric motors, gas turbines, or steam turbines. Choose the power source that aligns with your facility’s infrastructure and energy costs.
- Duty Cycle: Consider how frequently and for what duration the compressor will operate. Knowing the duty cycle helps determine the appropriate motor size and cooling capacity.
- Operating Environment: Factors like ambient temperature and humidity can impact the compressor’s performance.
- Maintenance Needs: Evaluate the ease of maintenance access and the availability of service providers in your area.
Rivair is a leading company specializing in compressed air solutions, including centrifugal compressor maintenance. The company has a team of skilled technicians who can provide the best compressor maintenance and other services according to your requirements and budget. The professionals use advanced diagnostic tools and techniques to identify and address any issues with your centrifugal compressor.
Final Thoughts
Centrifugal compressors are vital components in industrial air management systems. The efficient management of compressed air through advanced technologies like centrifugal compressors has become crucial for different industries. By investing in regular maintenance and partnering with reputable service providers like Rivair, you can make sure your centrifugal compressor continues to be the powerhouse driving your industrial processes.